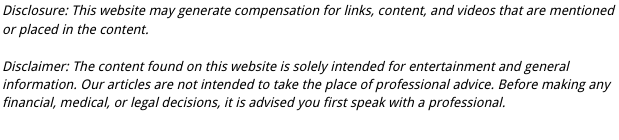

Computer numerical control (CNC) machines are the manufacturers best friend. CNC tooling is the process by which a computer automates the machining process to guarantee the same result every time. This makes CNC machines ideal for mass production.
CNC machines are able to move along a line or circular trajectory, thus providing 2D and 3D contouring. Their multiple axes are capable of simultaneous motion; to endmill in a circular trajectory, for instance, requires the machine to move simultaneously along both the X and Y axes. The machine can also move its cutting tool simultaneously along the X and Z axes, such as around the corner of a part to produce a fillet.
CNC milling machines cost around $60,000. A manual milling machine can be bought for $15,000, but the CNC machine often used in a lab setting for drilling wheel hubs costs closer to $60,000. Likewise, the tools needed for a CNC machine are twice as expensive as for a manual mill. Here are some of the tools you can expect to need when operating a CNC milling machine:
Tool Holders
You’ll need tools to attach other tools to your milling machine. If your machine has an R8 taper, these are the types of tool holders you’ll need to get started:
- Three to four R8 ER Collet Chucks: Just as a chuck on a hand drill or drill press is used to secure the drill bit to the drill’s shank, a collet chuck is needed to secure your endmill to the machine’s spindle. The size will depend on the size of your shank and endmill. For instance, you may want an ER32 for its ability to work with a wide range of shank sizes; or you may need a smaller, ER16 to accommodate small endmills for reaching spots too small for the ER32.
- ER Collets to coincide with your ER Collet Chucks: whichever Collet Chucks you buy, you’ll also need ER Collets to match. This may feel like a lot, but the good news is with an R8 ER collet you won’t need a drill chuck. ER collets are more efficient to use than drill chucks because they can hold a wider range of tools. If you’re operating a manual mill, a drill chuck might make sense, but for a CNC milling machine, it’s far too inefficient to need to touch off every time.
Cutting tools
- Endmills: Now that you’ve got your collet chucks and collets, you need the endmills to operate with them. You’ll want at least two of each size of endmill for maximum usability.
- Spot drills: With little or no flutes, spot drills are used for spotting holes for twist drills. You’ll use a spot drill to create an indent which will keep the twist drill from walking. Essentially, these are precision tools meant to insure the hole you create with your twist drill is where you want it.
- Center drills: Preferred over spot drills by some, center drills have a small pilot and larger countersinking area on the tip. They’re meant for drilling holes for the lathe center. They’re often cheaper than spot drills, but also more prone to breaking and are limited by their 60 degree angle.
- Twist drills: These are likely to be some of your most-used tools. A good twist drill is one that creates short, curled chips and readily evacuates them to prevent jamming. Whatever twist drills you purchase, keep them sharp and watch for signs of jamming during use. If you see bent chips coming out, for instance, your twist drill is likely jamming. The deeper your hole, the greater a problem jamming can become.
Tools to hold your work while milling
- T-Slot Clamping Kit: These kits are used to mount a vice. They can also be used to secure anything that can’t fit the vice itself.
- Vice: You’ll need either a Kurt-style vice or a grinder vice if your mill is small. These can be costly, but quality is a necessity. No matter how precise your spot drill is, it’ll do you no good if your work piece walks all over the table when you start drilling deep.
- Parallels: These can be used to hold projects higher on the jaws of your mill, allowing for greater accuracy.