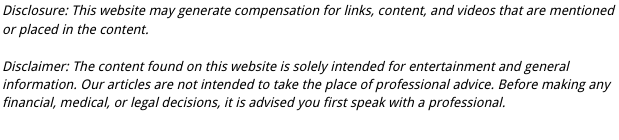
Air compressors and everything that goes along with them, from strut cushion clamps to compressor piping, are hugely important. Strut cushion clamps and other areas of successfully air compressing make a huge impact in industries all throughout the United States of America. An air compressor that is well kept up is essential for the continued function of a considerable amount of heavy equipment in United States industries and without it production of goods would fall significantly.
When it comes to manufacturing, air compressors and their parts, like cushion clamps and air compressor tubes, are nothing if not essential. In fact, statistics and studies have found that up to seventy percent of all manufacturing operations in the United States utilize air compressors on a regular, if not daily and hourly, basis. When an air compressing system that uses cushion clamps and the like is in use on such a regular day to day basis, it is very important (even crucial) that it receives the maintenance and servicing that it needs.
There are a number of problems that can arise with any typical air compressor, and these problems become more likely if the air compressors that are in use are not properly taken care of. For instance, a leak in one part of a compressed air system can have a considerably negative effect on the overall cost of the compressed air system, driving it up and up until the compressed air system is repaired. This can cost, in total, more than one thousand and two hundred dollars a year, added on to your energy bill. All of this can result from a hole in the air compressor or part of it (like the cushion clamps) that is no larger than one eighth an inch in diameter.
Pressure loss is also far too common in many air compressor systems throughout the United States and in the field of manufacturing. Pressure loss can be caused by a hole such as the one detailed above and go along with other problems happening to the system at the same time, but it can be an isolated issue in and off itself. A small degree of pressure loss is likely to happen at any time, but it is only once the pressure loss climbs above ten percent that it becomes more of a problem to be corrected by maintenance, servicing, and repair. Considerable pressure loss can increase your overall operating costs, as the system is no longer doing the job that it is designated for. Because of this, a noticeable pressure loss should be investigated as soon as it has been noticed. This way, the cause of the pressure drop can be discovered and rectified as soon as is possible for minimum loss to the company and operation.
Air compressors and their parts, like cushion clamps, are hugely important to many industries in the United States, particularly those operations that are involved in manufacturing. However, it is important to note that air compressors have the potential to waste good amounts of energy – and therefore, huge amounts of money for the company or business running the manufacturing operation. It is important to provide as regular servicing and maintenance as is needed (and truthfully, as is possible) for the air compressor in any manufacturing operation. This will help to fix problems before they become even more detrimental to the operation as well as keep problems from originating in the first place.