Ensure Your Compressed Air System Remains in Optimum Condition
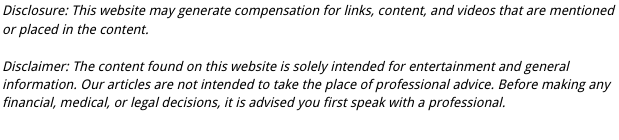

Were you aware that more than half of all manufacturers utilize compressed air systems? Recent figures indicate this this applies to around 70% of all businesses within this industry. Given this, it’s essential that these systems be kept in optimum condition to ensure that compressed air distribution flows properly.
When leaks occur within compressed air fittings or with other aspects of the compressed air piping materials, this can be expensive. When a one-eighth inch diameter hole is present within a 100 psi system, for example, this can waste over $1,200.00 worth of energy every year. In order to ensure that this doesn’t occur, it’s important to perform regular maintenance and take care of all noticeable leaks.
When pressure loss does occur with a properly designed system, it is usually less than ten percent of the compressor’s discharge pressure. This reading can be obtained from the gage, which is located on the compressor’s outlet. It is important to evaluate the distribution system if the pressure loss is more than ten percent. Once the area (or areas) causing this excessive pressure drop is identified, then this can be addressed. Operating costs can be reduced by 1.5% for every two pounds-per-square-inch pressure decrease.
The electrical energy that is used when operating a compressor is converted to heat. This can be as much as 80% to 90% of the overall energy being utilized. When a properly designed heat recovery unit is being used, 50% to 90% of this heat can be recovered to use for heating the air or water.
Does your compressed air system have an air receiver tank? If not, you may want to add one so that it can buffer any short-term demand changes. Furthermore, this can also reduce the on/off cycling of your compressor. It’s important to note that the tank will be sized to the compressor’s power. To provide you with an example, if you have a 50 hp air compressor, then you will need about a 50-gallon air receiver tank.
If you suspect that your existing compressor system has other issues, then it’s important to have it inspected and evaluated. While it may be that new pipes and/or tubing are needed, it’s also possible that you just need new cushion clamps. In addition to regular cushion clamps, your system may need strut cushion clamps.
As previously stated, it’s important to create the time to inspect and maintain your air compressor system. In this way, you won’t experience down time, wasted energy, or incur other unexpected costs. Furthermore, you’ll also be able to complete jobs in a timely fashion without needing to renegotiate deliver dates.